Introduction:
In industrial applications, pneumatic vacuum generators are vital in creating vacuum pressure for various processes. To ensure optimal performance and efficiency, it is crucial to understand the critical design considerations involved in selecting and utilizing these devices. This article addresses common user questions and provides insights into optimizing the performance of pneumatic vacuum generators.
Understanding the Operating Principles of Pneumatic Vacuum Generators
Pneumatic vacuum generators utilize compressed air to create pressure, enabling the suction and transfer of materials in industrial settings. These devices leverage the Venturi effect, where a high-speed compressed air flow creates a low-pressure area, resulting in a vacuum. The vacuum generator has three main components: the nozzle, diffuser, and body.
The nozzle accelerates the compressed air while the diffuser slows it down, creating the pressure difference required for generating a vacuum. The body encloses these components, ensuring efficient airflow and vacuum creation. Different types of vacuum generators, such as ejector-based and multi-stage, are available to cater to specific industrial requirements.
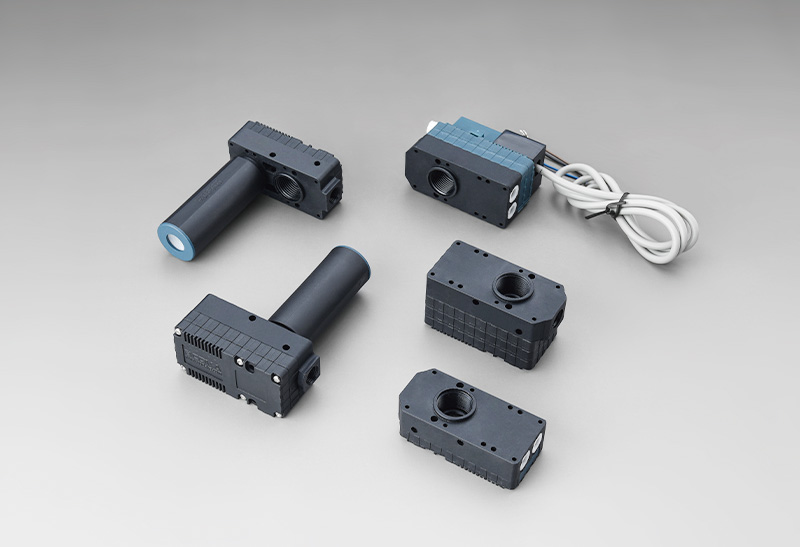
Key Design Considerations for Optimal Performance
To maximize the performance of a pneumatic vacuum generator, several design considerations must be taken into account:
- Flow rate and vacuum level requirements: Understanding the desired flow rate and vacuum level is crucial for selecting an appropriate vacuum generator. Manufacturers provide specifications indicating the maximum achievable vacuum level and the corresponding flow rates.
- Efficiency and energy consumption considerations: Energy efficiency is essential to reduce operating costs and environmental impact. Look for vacuum generators with high-efficiency ratings, such as those featuring optimized nozzle designs and integrated energy-saving features.
- Material selection for durability and resistance to harsh environments: Industrial applications often expose vacuum generators to challenging environments, including extreme temperatures, chemicals, and abrasive materials. Choosing a vacuum generator made of robust and corrosion-resistant materials ensures longevity and reliable performance.
- Noise reduction techniques: Industrial environments can be noisy, and excessive noise from vacuum generators can be disruptive and potentially harmful to workers. To minimize noise levels, look for vacuum generators with noise reduction features such as silencers or sound insulation materials.
- Maintenance and reliability factors: Regular maintenance is crucial to ensure pneumatic vacuum generators’ longevity and consistent performance. Consider models that offer easy access to critical components for inspection and maintenance. Additionally, select vacuum generators from reputable manufacturers known for their reliability and customer support.
Factors Influencing Performance Optimization
Several factors influence the optimization of a pneumatic vacuum generator’s performance:
- Proper sizing and selecting pneumatic components: Achieving optimal performance requires appropriately sized pneumatic components, including valves, fittings, and tubing. Ensuring compatibility and adequate integration between these components and the vacuum generator is vital.
- Understanding pressure drop and its impact on performance occurs when compressed air flows through the vacuum generator and associated piping. Excessive pressure drops can result in reduced vacuum levels and compromised performance. Considering the pressure drop across the system and selecting components that minimize this effect is crucial.
- Role of filters and separators in maintaining performance: Dust, debris, and moisture can negatively impact the performance and lifespan of a vacuum generator. Incorporating filters and walls in the system helps prevent clogging and protects the vacuum generator from potential damage.
- Considerations for integrating control systems and automation: Integrating vacuum generators with control systems and automation enhances operational efficiency. Features like adjustable vacuum levels, remote control capabilities, and real-time monitoring improve process control and optimization.
Best Practices and Recommendations for Users
To optimize the performance of a pneumatic vacuum generator in industrial applications, consider the following best practices and recommendations:
- Evaluate application requirements: Thoroughly assess the specific needs of your application, including required vacuum levels, flow rates, and environmental conditions. This information will guide you in selecting the most suitable vacuum generator for your application.
- Choose a reputable vacuum generator manufacturer: Selecting a reliable and reputable vacuum generator manufacturer is crucial. Look for manufacturers with a record of producing high-quality, durable, and efficient vacuum generators. Research customer reviews and seek recommendations from industry experts.
- Proper installation and setup: Follow the manufacturer’s instructions for installation, design, and connection of the vacuum generator. Ensure proper alignment and secure fittings to avoid air leaks that compromise performance. Regularly inspect connections and perform necessary maintenance tasks.
- Implement a preventive maintenance plan: Develop a preventative maintenance plan to ensure the long-term performance and reliability of the vacuum generator. As the manufacturer recommends, this plan should include regular inspections, cleaning, and replacement of worn-out components.
In conclusion, optimizing the performance of a pneumatic vacuum generator in industrial applications requires careful consideration of various design factors. Understanding the operating principles, selecting the right vacuum generator, and implementing best practices for installation, maintenance, and system integration is critical. By following these guidelines and partnering with reputable vacuum generator manufacturers, users can ensure efficient and reliable vacuum generation for their industrial processes.
Case Studies and Examples
To illustrate the successful optimization of pneumatic vacuum generator performance in industrial applications, let’s explore a few case studies:
- Automotive Manufacturing: In an automotive assembly line, a vacuum generator was selected based on the required flow rate and vacuum level for handling components during production. Integrating the vacuum generator with a centralized control system could adjust the vacuum level based on the specific operation, resulting in improved efficiency and reduced energy consumption.
- Packaging Industry: A vacuum generator manufacturer developed a specialized vacuum generator for a packaging company that required high vacuum levels for sealing containers. The vacuum generator incorporated advanced materials to withstand the corrosive environment of the packaging process. This optimized design enabled consistent vacuum levels, enhancing sealing and reducing product wastage.
- Pharmaceutical Production: A vacuum generator manufacturer collaborated with a pharmaceutical company to design a compact, portable vacuum generator for laboratory applications. The generator featured adjustable vacuum levels and integrated safety features. The optimized design allowed for precise control of the vacuum level during experiments, ensuring accurate results and improved productivity.
These case studies highlight how considering key design considerations and partnering with vacuum generator manufacturers can lead to successful performance optimization in various industrial applications.
Conclusion
Optimizing the performance of a pneumatic vacuum generator is essential for achieving efficient and reliable vacuum generation in industrial applications. By understanding the operating principles, considering design factors, and implementing best practices, users can select the right vacuum generator, enhance energy efficiency, ensure durability, reduce noise levels, and maximize performance.
When purchasing a pneumatic vacuum generator, it is crucial to collaborate with reputable manufacturers known for their expertise and quality products. Consulting experts and seeking their guidance will help address specific application requirements and challenges, ensuring the optimal performance of the chosen vacuum generator.
Remember, by prioritizing design considerations and leveraging the expertise of vacuum generator manufacturers, users can make informed decisions and achieve the desired performance for their industrial vacuum applications.
Thank you for reading, and feel free to contact vacuum generator manufacturers for further assistance and information.